How a Boiler Economizer Works
Boilers
A boiler burns fuel with oxygen to heat water to temperatures that transform it into steam. This generated steam is utilized for heating and numerous other industrial applications. Boiler fuels consist of wood, coal, oil and natural gas. The boiler combustion process results in exhaust gases that are vented through a flue (chimney). The downside of boiler design is that large amounts of heat can escape with the exhaust gases.
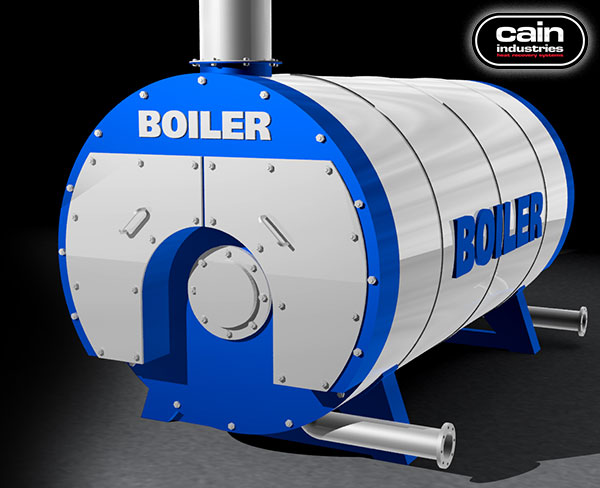
Most boilers have a combustion efficiency of 78-82%
If your spend $100,000 annually on fuel... $18,000 to $22,000 of that escapes up the exhaust stack in the form of lost heat!
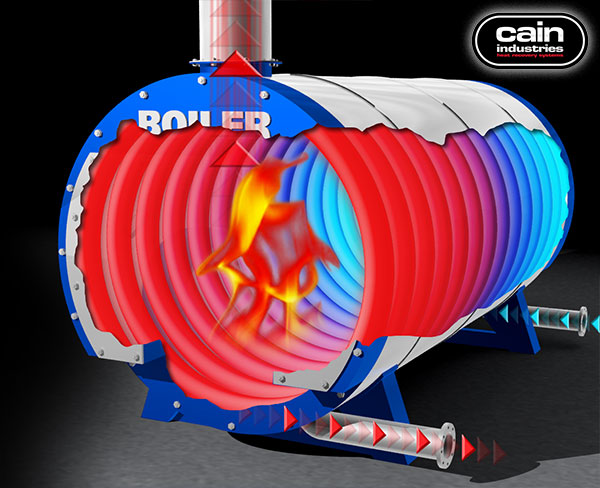
Boiler exhaust stack energy loss is typically 18-22%
Stack exhaust temperatures range from 350°F to 600°F.

Boiler Economizer
A boiler economizer is installed into the exhaust stream of the boiler. Exhaust waste heat is recovered by industrial finned tube that lines the inside of the economizer. The heat is transferred to the desired heat sink as it flows through the tubing: boiler feedwater, makeup water, process water and etc. The economizer reduces the overall fuel needed by the boiler for steam production and the resulting pollution. Economizers operate with virtually no maintenance.
Final stack exhaust temperatures are reduced to 150°F to 300°F.
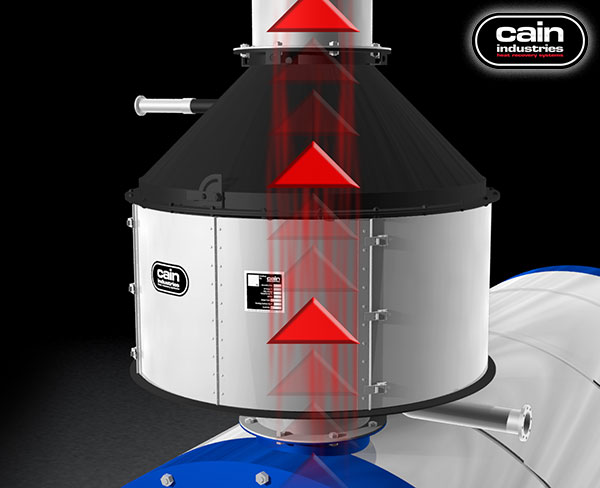
30-50% of available energy lost is recovered by a boiler economizer
You're now saving $6,000 to $10,000 of the lost energy from the earlier example! This level of return on investment typically pays back exhaust heat recovery equipment in 12 to 24 months.
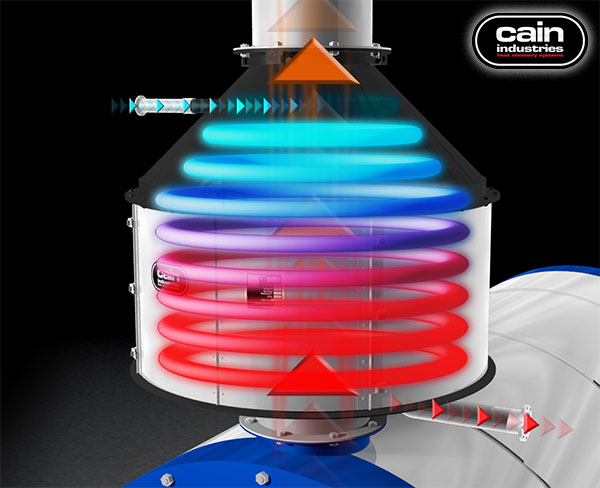