Heat Recovery Steam Generators | HRSG

Heat Recovery Steam Generators for Engines, Incinerators, Thermal Oxidizers and Catalytic Converters
Selecting the correct "Heat Recovery Steam Generator" (HRSG) for engine cogeneration (CHP) and other industrial waste heat systems involves much consideration. Important areas of focus are controlling/bypassing the exhaust heat, optimizing overall system performance, maintaining required operating pressures, the boiler size, weight and installation. Cain's HRSG families are specifically designed to address these concerns and more with standard design features not found in conventional waste heat boilers. Our equipment will adapt to any retrofit application or new installation. Contact our sales team to receive a comprehensive proposal and quotation engineered to meet your exact requirements (within 48 hours).
- Generates 99% Dry Steam
- 5 to 10 Minute Startup to Full Output
- 1/3 to 1/2 the Weight, Size and Footprint
- Integrated Full Exhaust Modulating Bypass
- "Explosion Proof" Heat Transfer Exchanger
- High Circulating Flow Minimizes Scale Buildup
- No Thermal Expansion Problems: Accepting Cold Water Boiler Feedwater
- Lowest "Pinch Point" Provides Greater Thermal Efficiency
- Tremendous fuel savings typically pay for installed equipment within 1 to 3 years of average use.
- Pollution reduction due to lowered annual fuel usage.
- Lower exhaust temperatures and significantly reduced sound output levels (final sound attenuation is typically 15 - 25 dBA).
- Hospitals
- Manufacturing Plants
- Schools
- Office Buildings
- Shopping Malls
- Drilling Platforms
- Oil & Gas Plants
- Marine
Heat Recovery Steam Generator for Engines
Cain Model: ESG1
The Only Heat Recovery Steam Generator in the World to Reach Full Steam from Startup in Less than 10 Minutes!
This fully packaged heat recovery steam generator is selected from 124 pre-engineered standard models with output capabilities of 20 to 300 boiler hp and operating steam pressures from 3 to 450 psig. The Cain ESG1 is shipped complete, ready for operating as either a primary or supplementary steam source.
The HRSG package is made up of three basic sections:- Finned tube heat transfer section
- Steam flash circulating drum assembly
- Modulating full port exhaust bypass system
Engine Exhaust Application
Capacity: 400kW to 7MW
Entering gas temps: 500°F to 1,250°F
Heat Sink Types: supplemental steam demand and/or primary steam source for steam heating or process steam
Operation and Control
The integral forced circulating water pump continually circulates high temperature water from the steam flash drum assembly to the heat transfer core assembly. BTU is transferred from the exhaust to a high flow superheated water/steam mixture. The superheated water is returned to the steam drum which contains dry pipe, baffles, and lance assemblies, where it flashes into 99% dry stream as its exits out to the system.
As the water is generated into steam and exits the boiler, the modulating boiler feedwater system controls continuous feedwater flow for constant drum water level control. Fail safe controls are built in for full exhaust bypass in the event of electrical or pneumatic loss.
The steam pressure controller maintains the operating steam pressure as it controls the modulating exhaust bypass assembly. This provides solid operating steam pressure under various operating steam load demands.
Quality Control
The Cain ESG1 is manufactured, tested, and stamped in accordance with the requirements of Section I of the ASME Boiler and Pressure Vessel Code, and National Board. Boiler trim includes all safety controls and alarms to meet state and federal codes. Final assembly, electrical wiring, and factory adjustments are completed under a strict set of guidelines.
The Cain heat recovery steam generator is an easy choice when compared to the "old technology" of a conventional firetube boiler:
- Completely self-contained package design reduces engineering, installation, and maintenance costs.
- Size requires only 1/2 the floor space and 1/2 the weight of conventional boilers, which reduces building size, structural support costs, and shipping costs.
- Ease of tube replacement requires no overhead cranes, special rigging, special crews, or extra roof height above the unit, while reducing down time.
- Many shapes and sizes are available to fit limited space and maintain performance requirements.
- Produces greater than 99% dry steam.
- Provides 100% turndown capability.
- 5–10 minutes from startup to full output.
- Integrated exhaust modulating bypass for safe automatic steam control.
- Explosion-proof heat transfer exchanger.
- Low friction loss for minimum static exhaust back pressure.
- High circulating flow to minimize scale buildup.
- No thermal expansion concerns with cold boiler feedwater.
- Performance aimed at the lowest pinch point in the industry (final leaving exhaust temperature minus operating steam temperature) for maximum thermal efficiency.
Our HRSG requires only the following connections for a cost effective installation:
- Steam Outlet
- Exhaust Flange Inlet and Outlet
- Single Main Power
- Single Main Blowdown
- Feedwater Inlet
- Pneumatic Control Air
- Cooling Water Inlet and Outlet
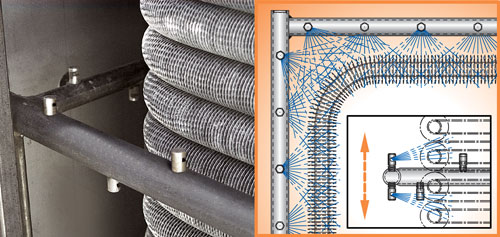
Automatic or Manual Sootblower (optional)
Maintain Peak Performance
The exclusive Cain Industries Timed Automatic Sootblower design is applied to combustion sources where the sulfur content is high and/or combustion efficiency is poor. When a soot layer accumulates on the heating surface to a thickness of 1/8", fuel consumption is increased by 8.5%. The sootblower is also applied when it is not cost-effective to open inspection doors and clean the exchanger by other means. The sootblower system will continually keep the heating surface at a high performance level and eliminate the day-to-day operator expense and engine down time.
The blowdown sequence occurs while the engine is in full operation and is fully adjustable. The special flood-jet type nozzles achieve maximum cleaning velocity using steam or air as discharged through an electric control valve (included). Together they form a "continuous knife edge concentrated spray pattern" surrounding the heating surface. This "ring nozzle assembly" as attached to a manifolded flexible steel hose assembly, is powered up and down by a pneumatic drive cylinder. Dual timing relays allow complete control for 30 second cycle duration and intervals specific to each application. Final results are controlled double cleaning action, insuring that the maximum BTU recovery and anticipated savings are achieved.
Optional Components
Continuous Blowdown with Intermittent Conductivity Sampling Assembly
Maximize boiler efficiency by periodically sampling surface blowdown water and controlling total dissolved solids. Maintaining optimal levels of concentrations will control the costs of water, energy and chemicals. Assembly includes: motorized valve, probe and piping assembly.
Hinged Access Door for Full Heating Surface Inspection
Hinged access doors are considered when firing with fuel oil and/or incomplete combustion requiring full access on a regular basis for manual cleaning. A hinged access door can be incorporated for 100% finned tube viewing and attention.
Heat Recovery Steam Generator for Incinerators, Thermal Oxidizers and Catalytic Converters
Cain Model: ESG
Cold Start to Full Steam in Less than 10 Minutes!
This HRSG is an unfired fully automatic, skid mounted packaged steam generator combining a finned tubing heat transfer section, steam flash circulating drum assembly, and full exhaust bypass. Where low or high pressure steam output demand is a necessity, the HRSG in terms of recovered BTU/hr and its use, is a more valuable alternate selection to liquid or air preheat exchangers. The design allows for flexibility in heat transfer (explosion proof) output, lightweight design and compactness for lower installation costs, and will offer the greatest thermal efficiency.
Cain's heat recovery steam generator accommodates outputs from 20 to 500 boiler horsepower with operating steam pressures ranging from 3 to 450 PSIG. Engineering design consideration has been given to complexities and flexibility requirements of steam generation, and retrofitting the engine and fume incineration market. Important areas of concern are: controlling and bypassing waste heat, optimum performance selection, operating pressures, size, weight, and ease of installation. Our HRSG addresses concerns with standard design features important to the designer, packager, and customer which are not usually found in conventional waste heat firetube boilers.
The extremely lightweight, compact design includes three basic sections: the fin tube heating surface, steam flash drum assembly, and a modulating full-port exhaust bypass pre-piped and wired for ease of installation and minimal customer connections. The integral circulating pump continually circulates water to the heat transfer section recovering BTU from the exhaust, and back to the steam drum assembly where the water is flashed to steam. Coupled with the HRSG's capacity to produce and control supplemental or primary steam output, it's unique design allows for full output in approximately 10 to 15 minutes and is fully automatic under fluctuating loads. The HRSG is a packaged forced circulation watertube design, manufactured and tested in accordance with the requirements of Section VIII, Division I of the ASME Boiler and Pressure Vessel Code, and stamped to the appropriate section.
Combustion Sources
Incinerators, thermal oxidizers and catalytic converters
Exhaust Application
Capacity: 1,000 to 50,000 SCFM
Entering Gas Temps: 600°F to 1,600°F
Heat Sink Types: supplemental steam demand and/or primary steam source for steam heating or process steam
- Steam Flash Drum Assembly
- Inspection and Tube Removal Door
- Fully Modulating Internal Exhaust Bypass
- Circulating Pump Assembly
- Pneumatic Modulating Damper Actuator
- Control Panel Assembly
- Boiler Blowdown Systems
- Boiler Feedwater Economizer
- Boiler Feed Condensate Return Systems
Optional System Equipment
Components for Complete Systems
Cain Industries' engineering team is available to propose the proper system components at competitive pricing. Upon review of your application, you can expect our proposal within 48 hours. It will include professionally engineered details showing equipment costs, savings analysis, computer generated economizer performance, CAD dimensional drawings, flow schematics, warranty, and a performance guarantee.
No matter how small the micro-turbine or how large the engine, Cain Industries has the heat transfer equipment, optional components and years of experience to provide the best solution.
- Remote digital indicators and control packages
- Pre-piped skid mounted circulation pump system packages
- Boiler blowdown assemblies
- Valves: steam stop, shut-off, relief, vent, drain and check
- Pressure or temperature control valves
- Bi-metallic or mercury thermometers
- Expansion joints
- Explosion hatch relief ports
- Tanks: storage or expansion
- Bypass damper actuators: pneumatic or electric, on/off or modulating, air or spring failsafe return
Ebullient Steam Generators from Engine Jacket Water
The Exhaust Cooling Steam Generator (ECSG) as designed to produce low pressure steam (15 PSIG and under) from engine jacket water via natural circulation. They are available in a variety of tank sizes for horizontal or vertical installations. Standard design includes: ASME stamped steam flash tank built in accordance with Sec.VIII Div.I; shipped as a packaged unit including continuous water level feed control with low water cutoff, auxiliary low water cutoff, excess steam pressure switch, gauge glass assembly, surface and main blowdown assembly, vent valve, steam safety valve, steam pressure gauge, wall or floor mount. Basic customer connections for ease of installation include: 150# steam outlet, 150# water outlet, 150# water/steam inlet, NPT Blowdown, and NPT Boiler feedwater. The unit shall be pre-piped and wired for a single 120v 1ph 60hz customer power connection.
Boiler Feedwater Tank Assembly
Cain Boiler feedwater systems are available in a variety of tank sizes, feedwater pump configurations, and optional water treatment assemblies. Packaged assemblies include: heavy wall tank as mounted on a 5' high rectangular tube structural steel stand with water level controls and low water cutout, gauge glass and thermometer, magnesium anode; (2) 2" NPT vents; 2" NPT condensate return; 1" NPT drain with shut off valve; Duplex or Triplex boiler feedwater pump system; electrical control panel fully pre-wired with fused disconnect switches, magnetic starters, manual start-stop switches and indicating run lights for feedwater pumps and alarms; all interconnecting wiring from electrical control panel to each component, optional chemical feed system, and/or automatic water softening system; all interconnecting bypass piping, valves, gauges, fittings, etc. Primed, painted, and tested package is a complete, properly functioning assembly, ready for the customer’s primary connections of water, condensate return, and electricity.
Our Uniquely Designed Exhaust Gas Bypass Valves
Cain Industries offers total exhaust gas control with high temperature modulating bypass and shut off valves. The valve assemblies offer precise exhaust temperature control and/or the design capability for exhaust isolation. Sizes ranging from 4" to 40" diameter are available in carbon steel and stainless steel for all engine temperatures. All valves are available with either electric or pneumatic control actuation and emergency fail safe features.
Steam Table
The following steam table plays a vital role in determining exact steam process requirements:
Gauge PSI | Temp. °F | Volume cu. ft./lb. | Total Heat Above 32°F/lb. | ||
---|---|---|---|---|---|
Sensible Heat hf | Latent Heat hfg | Total Heat hg | |||
0 | 212.0°F | 26.80 | 180.1 | 970.3 | 1,150.4 |
1 | 215.5°F | 25.13 | 183.6 | 968.1 | 1,151.7 |
2 | 218.7°F | 23.72 | 186.8 | 966.0 | 1,152.8 |
3 | 221.7°F | 22.47 | 189.8 | 964.1 | 1,153.9 |
4 | 224.5°F | 21.35 | 192.7 | 962.3 | 1,155.0 |
5 | 227.3°F | 20.34 | 195.5 | 960.5 | 1,156.0 |
6 | 229.9°F | 19.42 | 198.2 | 958.8 | 1,157.0 |
7 | 323.4°F | 18.58 | 200.7 | 957.2 | 1,157.9 |
8 | 234.9°F | 17.81 | 203.2 | 955.6 | 1,158.8 |
9 | 237.2°F | 17.11 | 205.6 | 954.1 | 1,159.7 |
10 | 239.5°F | 16.46 | 207.9 | 952.5 | 1,160.4 |
11 | 241.7°F | 15.86 | 210.1 | 951.1 | 1,161.2 |
12 | 243.8°F | 15.31 | 212.2 | 949.7 | 1,161.9 |
13 | 245.9°F | 14.78 | 214.3 | 948.3 | 1,162.6 |
14 | 247.9°F | 14.31 | 216.4 | 946.9 | 1,163.3 |
15 | 249.8°F | 13.86 | 218.3 | 945.6 | 1,163.9 |
16 | 251.7°F | 13.43 | 220.3 | 944.3 | 1,164.6 |
17 | 253.6°F | 13.03 | 222.2 | 943.0 | 1,165.2 |
18 | 255.4°F | 12.66 | 224.0 | 941.8 | 1,165.8 |
19 | 257.1°F | 12.31 | 225.7 | 940.6 | 1,166.3 |
20 | 258.8°F | 11.98 | 227.5 | 939.5 | 1,167.0 |
21 | 260.5°F | 11.67 | 229.2 | 938.3 | 1,167.5 |
22 | 262.2°F | 11.37 | 230.9 | 937.2 | 1,168.1 |
23 | 263.8°F | 11.08 | 232.5 | 936.1 | 1,168.6 |
24 | 265.4°F | 10.82 | 234.1 | 935.0 | 1,169.1 |
25 | 266.9°F | 10.56 | 235.6 | 934.0 | 1,169.6 |
30 | 274.1°F | 9.45 | 243.0 | 928.9 | 1,171.9 |
35 | 280.7°F | 8.56 | 249.8 | 924.2 | 1,174.0 |
40 | 286.8°F | 7.82 | 256.0 | 919.8 | 1,175.8 |
45 | 292.4°F | 7.20 | 261.8 | 915.7 | 1,177.5 |
50 | 297.7°F | 6.68 | 267.2 | 911.8 | 1,179.0 |
55 | 302.7°F | 6.23 | 272.4 | 908.1 | 1,180.5 |
60 | 307.3°F | 5.83 | 277.2 | 904.6 | 1,181.8 |
65 | 311.8°F | 5.49 | 281.8 | 901.3 | 1,183.1 |
70 | 316.4°F | 5.18 | 286.2 | 898.0 | 1,184.2 |
75 | 320.1°F | 4.91 | 290.4 | 894.8 | 1,185.2 |
80 | 323.9°F | 4.66 | 294.4 | 891.9 | 1,186.3 |
85 | 327.6°F | 4.44 | 298.2 | 889.0 | 1,187.2 |
90 | 331.2°F | 4.24 | 301.9 | 886.1 | 1,188.0 |
95 | 334.6°F | 4.06 | 305.5 | 883.3 | 1,188.8 |
100 | 337.9°F | 3.89 | 308.9 | 880.7 | 1,189.6 |
105 | 314.1°F | 3.74 | 312.3 | 878.1 | 1,190.4 |
110 | 344.2°F | 3.59 | 315.5 | 875.5 | 1,191.0 |
115 | 347.2°F | 3.46 | 318.7 | 873.0 | 1,191.7 |
120 | 350.1°F | 3.34 | 321.7 | 870.7 | 1,192.4 |
125 | 352.9°F | 3.23 | 324.7 | 868.3 | 1,193.0 |
130 | 355.6°F | 3.12 | 327.6 | 865.9 | 1,193.5 |
135 | 358.3°F | 3.02 | 330.4 | 863.7 | 1,194.1 |
140 | 360.9°F | 2.93 | 333.1 | 861.5 | 1,194.6 |
145 | 363.4°F | 2.84 | 335.8 | 859.3 | 1,195.1 |
150 | 365.9°F | 2.76 | 338.4 | 857.2 | 1,195.6 |
155 | 368.3°F | 2.68 | 340.9 | 855.0 | 1,195.9 |
160 | 370.6°F | 2.61 | 343.4 | 853.0 | 1,196.4 |
165 | 372.9°F | 2.54 | 345.9 | 850.9 | 1,196.8 |
170 | 375.2°F | 2.47 | 348.3 | 848.9 | 1,197.2 |
175 | 377.4°F | 2.41 | 350.7 | 846.9 | 1,197.6 |
180 | 379.5°F | 2.35 | 353.0 | 845.0 | 1,198.0 |
185 | 381.6°F | 2.30 | 355.2 | 843.1 | 1,198.3 |
190 | 383.7°F | 2.24 | 357.4 | 841.2 | 1,198.6 |
195 | 358.8°F | 2.19 | 359.6 | 839.2 | 1,198.8 |
Gauge PSI | Temp. °F | Volume cu. ft./lb. | Total Heat Above 32°F/lb. | ||
---|---|---|---|---|---|
Sensible Heat hf | Latent Heat hfg | Total Heat hg | |||
200 | 387.8°F | 2.14 | 361.8 | 837.5 | 1,199.3 |
205 | 389.8°F | 2.09 | 364.0 | 835.7 | 1,199.7 |
210 | 391.6°F | 2.04 | 366.0 | 833.9 | 1,199.9 |
215 | 393.6°F | 2.00 | 368.0 | 832.1 | 1,200.1 |
220 | 395.4°F | 1.96 | 370.0 | 830.4 | 1,200.4 |
225 | 397.2°F | 1.92 | 372.0 | 828.6 | 1,200.6 |
230 | 399.0°F | 1.88 | 374.0 | 826.9 | 1,200.9 |
235 | 400.8°F | 1.85 | 375.9 | 825.2 | 1,201.1 |
240 | 402.6°F | 1.81 | 377.7 | 823.6 | 1,201.3 |
245 | 404.4°F | 1.78 | 379.6 | 821.9 | 1,201.5 |
250 | 406.0°F | 1.74 | 381.5 | 820.2 | 1,201.7 |
255 | 407.7°F | 1.72 | 383.3 | 818.6 | 1,201.9 |
260 | 409.3°F | 1.69 | 385.1 | 817.0 | 1,202.1 |
265 | 410.9°F | 1.66 | 386.9 | 815.4 | 1,202.3 |
270 | 412.5°F | 1.62 | 388.6 | 813.8 | 1,202.4 |
275 | 414.1°F | 1.60 | 390.4 | 812.2 | 1,202.6 |
280 | 415.8°F | 1.57 | 392.1 | 810.6 | 1,202.7 |
285 | 417.2°F | 1.54 | 393.7 | 809.1 | 1,202.8 |
290 | 418.8°F | 1.52 | 395.3 | 807.6 | 1,202.9 |
295 | 420.3°F | 1.50 | 397.1 | 806.1 | 1,203.2 |
300 | 421.7°F | 1.47 | 398.7 | 804.6 | 1,203.3 |
305 | 423.1°F | 1.45 | 400.3 | 803.1 | 1,203.4 |
310 | 424.6°F | 1.43 | 401.9 | 801.6 | 1,203.5 |
315 | 425.2°F | 1.41 | 403.5 | 800.1 | 1,203.6 |
320 | 427.5°F | 1.39 | 405.0 | 798.6 | 1,203.6 |
325 | 428.9°F | 1.37 | 406.6 | 797.2 | 1,203.8 |
330 | 430.3°F | 1.35 | 408.1 | 795.7 | 1,203.8 |
335 | 431.6°F | 1.33 | 409.6 | 794.3 | 1,203.9 |
340 | 433.0°F | 1.31 | 411.1 | 792.9 | 1,204.0 |
345 | 434.3°F | 1.29 | 412.6 | 791.5 | 1,204.1 |
350 | 435.7°F | 1.27 | 414.0 | 790.1 | 1,204.1 |
355 | 437.0°F | 1.26 | 415.5 | 788.7 | 1,204.2 |
360 | 438.3°F | 1.24 | 416.9 | 787.3 | 1,204.2 |
365 | 439.5°F | 1.22 | 418.4 | 785.9 | 1,204.3 |
370 | 440.8°F | 1.21 | 419.8 | 784.5 | 1,204.3 |
375 | 442.0°F | 1.19 | 421.2 | 783.2 | 1,204.4 |
380 | 443.3°F | 1.18 | 422.6 | 781.9 | 1,204.5 |
385 | 444.6°F | 1.16 | 423.9 | 780.6 | 1,204.5 |
390 | 445.8°F | 1.15 | 425.3 | 779.2 | 1,204.5 |
395 | 447.1°F | 1.13 | 426.7 | 777.8 | 1,204.5 |
400 | 448.2°F | 1.12 | 428.0 | 776.5 | 1,204.5 |
405 | 449.4°F | 1.11 | 429.3 | 775.3 | 1,204.6 |
410 | 450.5°F | 1.09 | 430.7 | 773.9 | 1,204.6 |
415 | 451.8°F | 1.08 | 432.0 | 772.6 | 1,204.6 |
420 | 452.8°F | 1.07 | 433.3 | 771.3 | 1,204.6 |
425 | 453.9°F | 1.06 | 434.5 | 770.1 | 1,204.6 |
430 | 445.2°F | 1.04 | 435.8 | 768.8 | 1,204.6 |
435 | 456.3°F | 1.03 | 437.1 | 767.5 | 1,204.6 |
440 | 457.3°F | 1.02 | 438.4 | 766.2 | 1,204.6 |
445 | 458.4°F | 1.01 | 439.6 | 765.0 | 1,204.6 |
450 | 459.5°F | 1.00 | 440.9 | 763.7 | 1,204.6 |
455 | 460.6°F | 0.99 | 442.1 | 762.5 | 1,204.6 |
460 | 461.7°F | 0.98 | 443.3 | 761.2 | 1,204.5 |
465 | 462.7°F | 0.97 | 444.5 | 760.0 | 1,204.5 |
470 | 463.8°F | 0.96 | 445.7 | 758.8 | 1,204.5 |
475 | 464.9°F | 0.95 | 446.9 | 757.6 | 1,204.5 |
480 | 466.0°F | 0.94 | 448.1 | 756.3 | 1,204.4 |
485 | 467.1°F | 0.93 | 449.3 | 755.1 | 1,204.4 |
490 | 468.0°F | 0.92 | 450.5 | 753.8 | 1,204.3 |
495 | 469.0°F | 0.91 | 451.7 | 752.6 | 1,204.3 |