Condensing Economizers
Harnessing the power of sensible and latent exhaust heat recovery for even greater energy savings.
Cain Industries condensing heat exchangers are the most effective means of exhaust heat recovery. Natural gas or propane combustion gases are channeled through rows of corrosion-resistant finned tube that line the inside of our uniquely designed exchangers. Cold water typically flows through the tubing to absorb the waste heat. A cold "heat sink" absorbs sensible and latent heat the best... The colder the better!
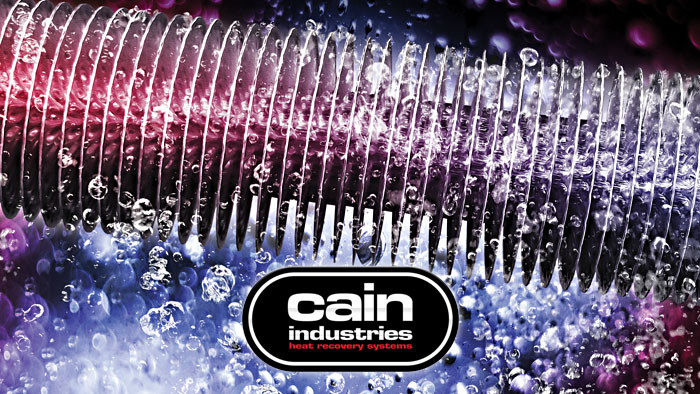
Sensible heat transfers to the heat sink without change in phase. Valuable latent heat is recovered from water vapor contained in the exhaust gases as it changes phase from a gas to liquid state. Microscopic water droplets form at the contact point where exhaust temperatures drop to dew point or below on the heat transfer surface. Large volumes of cold water produce the greatest amount of condensation. Droplets rapidly concentrate to form streams of running water that flow from the condensing fin tube. The gas-to-liquid transformation releases roughly 1,000 BTUs of latent heat for every pound of water created. The more water generated, the more latent heat recovered! Capturing both sensible and latent heat drastically increases exhaust heat recovery efficiency.
Cain Industries manufactures condensing heat exchangers for steam boilers, hot water boilers and most natural gas combustion applications where a cold water heat sink is prevalent. All condensation is safely captured and drained away from the exchanger to the sewer, protecting the combustion source. Heat sinks consist of boiler feedwater, makeup water, hot water return, hot water storage tank, condensate tank, swimming pool and various types of process water.
Cain Industries offers single and two-stage condensing heat exchanger series. Single-stage condensers are used where large supplies of cold water are available, ideally below ambient temperature. Our two-stage exchanger's unique construction provides heat transfer for two independent heat sinks where less cold water is available... Designed to manage the greatest entering temperature difference between the exhaust and liquid temperature. Boiler feedwater is preheated in the primary stage with prevailing heat exposure, while makeup water is heated in the secondary stage with lowered exhaust temperatures. Cain Industries condensing exchanger product lines collectively offer the best engineered solutions for applications with targeted heat recovery yields.
Designed, engineered, and hand-built in the USA, Cain Industries manufactures the largest selection of exhaust heat recovery products in the industry. Years of research and development have resulted in industrial heat exchangers that perform consistently with minimum maintenance and provide dramatic fuel savings over the life of the equipment.
We guarantee the performance of every condensing heat exchanger we build!
CXL | Single Stage Condensing Economizer

The CXL Single Stage Condensing Economizer is specifically designed to recover sensible heat from within the exhaust and, more importantly, to also recover additional valuable latent heat as the exhaust is condensed. Typically the recovered heat will be transferred to the cold makeup or process water, thereby increasing the overall efficiency and lowering the fuel demand. As the exhaust temperature is dramatically reduced to 120°F to 170°F, resulting condensation is safely captured and drained from the economizer and away from the boiler.
Combustion Sources
Steam boilers, hot water boilers, and hot oil heaters with inputs up to 250,000,000 BTU/hr. (natural gas fired)
Boiler Exhaust Application
Capacity: up to 250,000 lb/hr steam
Entering Gas Temps: 300°F to 800°F
Heat Sink Types: makeup water and process water
- Internal expansion design
- Mounting flanges for bolting to mating flanges/adapters
- Condensate drain catch ring assembly
- 12 gauge stainless steel exterior
- Stainless steel interior
- 2" factory insulation
- Removable access doors
- Stainless steel bypass
- Stainless steel header manifold for high liquid flow
- Compression fittings between finned tubes and the liquid manifolds for easy tube removal that requires no welding
DXL | Two Stage Condensing Economizer
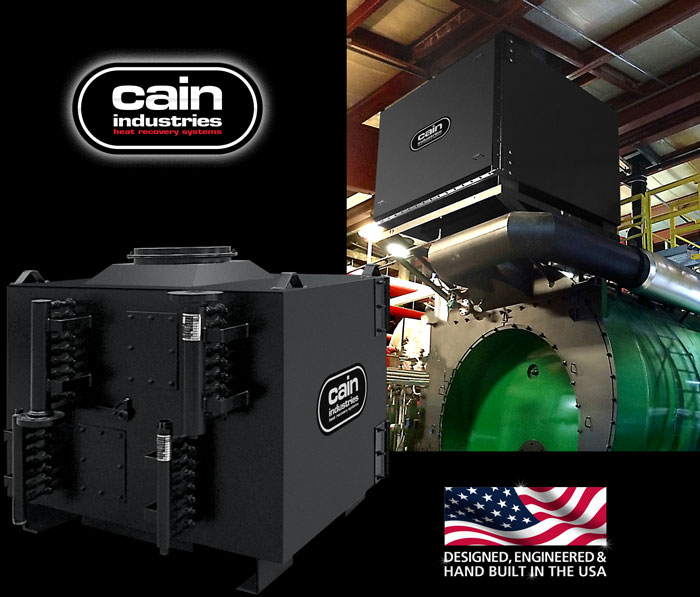
The DXL Two Stage Condensing Economizer is specifically designed to recover sensible heat from within the exhaust and, more importantly, to also recover additional valuable latent heat as the exhaust is condensed. What makes the DXL Boiler Economizer unique is that it recovers heat in two stages. The first stage will preheat boiler feedwater and the second stage will preheat boiler makeup water. Final exhaust temperatures leaving typically range from 120°F to 170°F. This recovered heat will be transferred to feedwater and makeup water, thereby increasing the overall efficiency and lowering the fuel demand.
Combustion Sources
Steam boilers, hot water boilers, and hot oil heaters with inputs up to 250,000,000 BTU/hr. (natural gas fired)
Boiler Exhaust Application
Capacity: up to 250,000 lb/hr steam
Entering Gas Temps: 300°F to 800°F
Heat Sink Types: boiler feedwater, makeup water, hot water return, hot water storage tank, condensate tank, process water
- Internal expansion design
- Mounting flanges for bolting to mating flanges/adapters
- Condensate drain catch ring assembly
- 12 gauge stainless steel exterior
- Stainless steel interior
- 2" factory insulation
- Removable access doors
- Stainless steel bypass
- Stainless steel header manifold for high liquid flow
- Compression fittings between finned tubes and the liquid manifolds for easy tube removal that requires no welding